The Methodology
Revolutionising functionalisation of textiles, BioFibreLoop project will develop and optimise biomimetic laser-based surface functionalisation for market entry.
Have a look at “the biofibreloop” to learn more about the different aspects of our project.
Besides the development and upscaling of the processes, the preparation for market entry will be achieved by focusing on safety and sustainability assessment, strong engagement and collaboration with key stakeholders to foster the acceptance and adoption of our solutions. The validation of our business case and exploitation strategy ensure a quick market uptake.
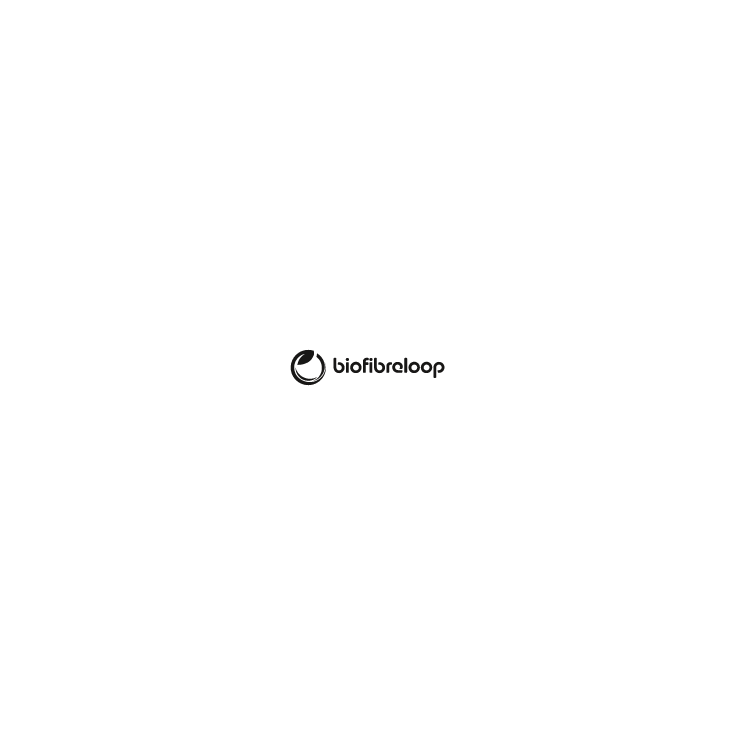
The approach prioritises safety and sustainability through life cycle and techno-economic assessments, risk mitigation via SSbD (safe and sustainable by design) principles, and strategies to enhance recyclability, circularity, and resource efficiency. It is also planned to use sensors in the process and finalised products which can give valuable insights in product performance, environmental impact and user experience.
If you are interested in our project and in our technologies, reach out to us!
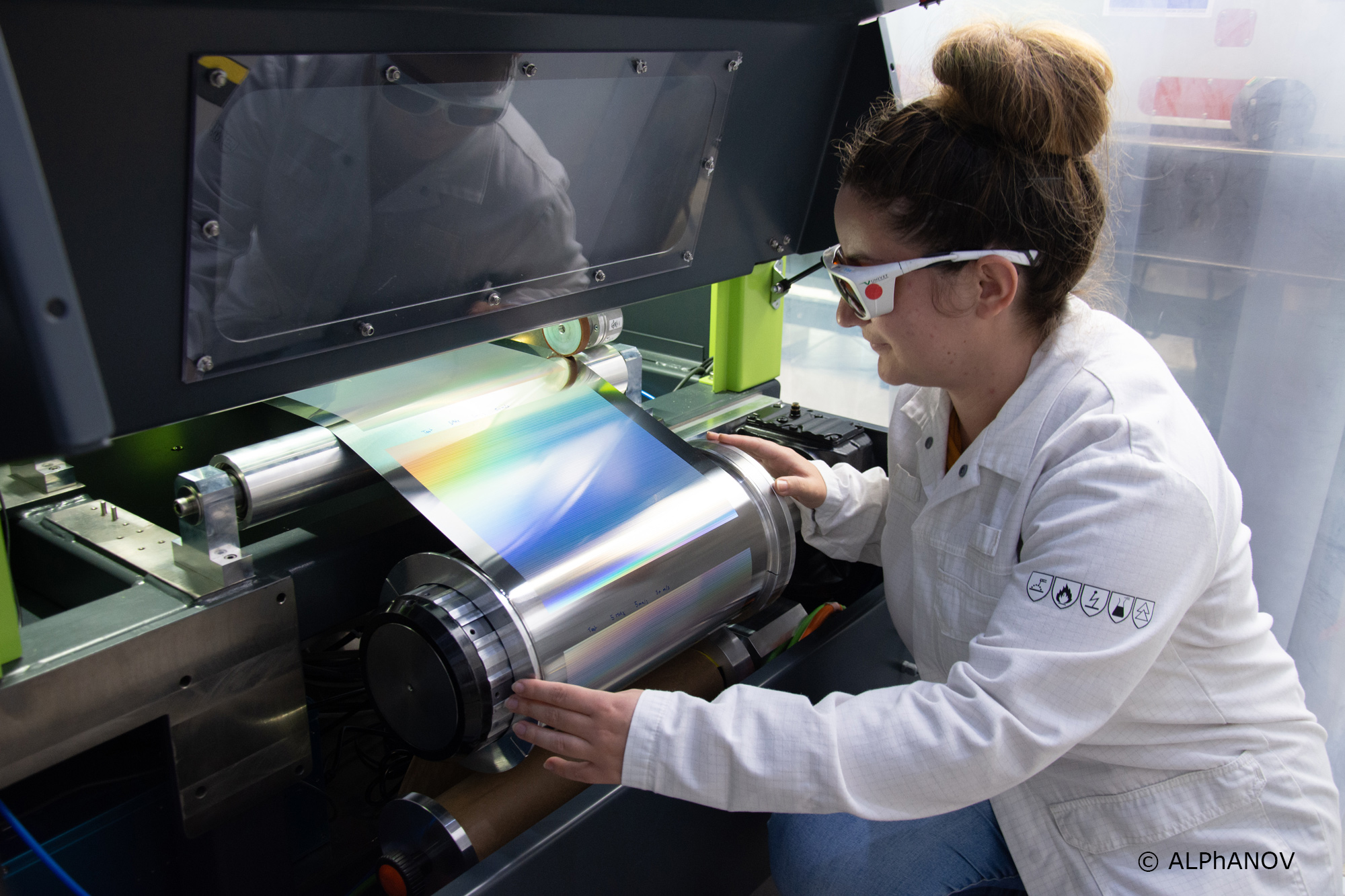
Roll to roll texturing of metallic coils by femtosecond laser. ©ALPhANOV